Japanese contractor Shimizu Corporation has introduced a new technique for developing curved glass facades with a high degree of accuracy. This method “significantly expands architectural freedom by enabling the fabrication of glass panels with complex bends and twists, a feat that was difficult to achieve before,” said the company.
The rise of a computational design method has driven demand for dynamic architectural glass with curved geometry, explained Shimizu. “However, such glass facades are much more expensive and time-consuming to make compared to flat glass facades. This is because they require a more complex support structure for glass panels and because a higher level of precision is required when producing the components and fitting the panels.
“The cold bending method is sometimes used as a low-cost method for curved glass facades. Under this method, glass panels housed in curtain wall units are forcibly bent and twisted at the construction site and then fitted at the target location. However, this method allows only a limited degree of curvature and thus precludes the more geometrically complex designs that many architects desire.”
With the technique developed by Shimizu, curved glass panels made from chemically strengthened laminated glass are bonded to the support structure by point-fixed glazing. The company said this method provides an optimal support structure, ensuring constructability and construction quality.
For the support structure, the design team follows a generative design process and uses a metal 3D printer to create a metal structure that best fits the curvatures of the glass, explained Shimizu. “More specifically, they use a generative design method to explore design ideas until they derive the most effective support structure for ensuring the structural integrity of the adhesive point-fixings.
“Next, they input this design into the 3D printer, which fabricates the design from metal powders. Finally, a 3D scan is performed on the printed structure to check its accuracy and they start the construction. During construction, the glass panels are attached to the support structure using a structural adhesive, which helps ensure construction accuracy and streamlines the fitting process.”
To test the new technique, Shimizu built a mockup (3 m x 5 m) at the Shimizu Institute of Technology, which has demonstrated the constructability of the design. According to the company, it will use mockups for the actual-size performance exam to test resilience against earthquakes and strong wind. Once the resilience is proven, the company will start offering the technique in real construction projects.
Images: Shimizu

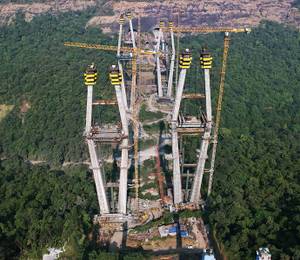
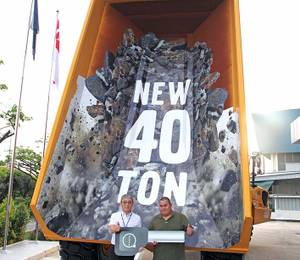
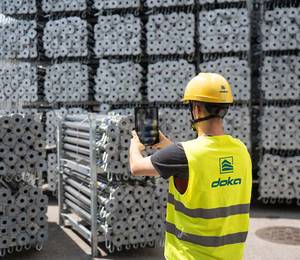
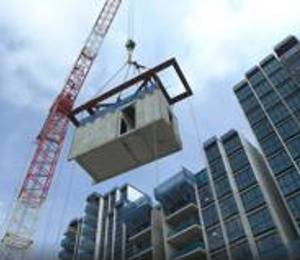
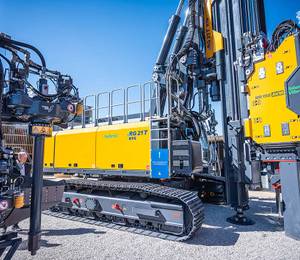
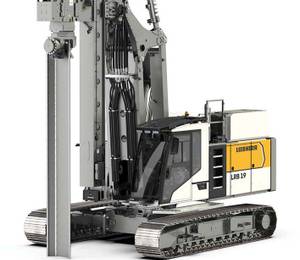