Bauer Maschinen GmbH has introduced an innovative cutting system, Bauer Cube System, which was developed in collaboration with the Belgian tunnel construction expert Denys. This new solution is expected to open up entirely new opportunities for the future construction of diaphragm walls.
“It is designed as an electrically powered cutting system which builds on a great deal of proven expertise from Bauer, but features an entirely new construction,” said Dr Ruediger Kaub, managing director of Bauer Maschinen GmbH.
The entire system was developed precisely in container dimensions, making it unique, said Bauer. This means it can be used without any problem in microtunnels with small diameters of just 3.8 m, for example.
“Imagine you are planning a new subway line in a densely populated city. Ideally, you want to plan the new line to allow passengers to get on and off exactly where they want to go. This means that the new subway stations need to be located exactly where there are large office complexes, a large shopping centre or the city centre. But precisely in such locations, it would be very difficult or even impossible to build these subway stations with the technology available to date,” explained Dr Kaub.
“It is now possible thanks to our Bauer Cube System, which can be used exactly where the new subway stations need to be constructed: underground, below the existing buildings. This opens up entirely new opportunities for designers and architects.”
With the new system, underground expansion of cities, setting up drinking water storage, or transferring cloud servers below ground along with the necessary cooling technology are all conceivable applications. “These examples demonstrate the enormous potential of our cube system,” continued Dr Kaub.
The Bauer Cube System offers several advantages. For one, the impact of construction sites on traffic, businesses and residents are minimised. This is because the minimally invasive system only requires a comparatively small access point to an existing microtunnel or auxiliary tunnel. The actual work is carried out underground, essentially invisibly.
In addition, the electric drive system considerably reduces the ecological disturbance of a cutting site. And when it comes to logistics, the system’s compact dimensions pose another advantage. Its individual elements can be easily transported to their place of deployment as conventional containers. As a result, the Bauer Cube System also sets new standards in terms of sustainability.
“Last but not least, I would particularly like to emphasise the trusting and highly constructive collaboration with our strategic partner Denys as well as our specialists within the Group,” said Dr Kaub. “During the development phase, this collaboration delivered crucial input that allowed us to examine nearly every aspect of process engineering, mechanical engineering, logistics or external influences on the site in advance. Based on this research, many ideas were incorporated into the system at an early stage of development.”
The first successful tests of the prototype under the most realistic conditions possible have already been conducted on the Bauer plant grounds in Aresing, near the company’s headquarters in Schrobenhausen, Germany. This test phase will continue for the next four to six months, which in principle means that an anticipated practical application will be feasible towards the end of 2021.
Images: Bauer Group
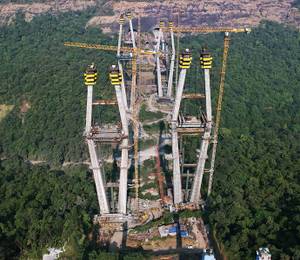
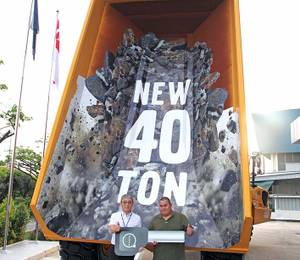
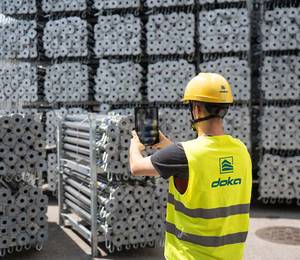
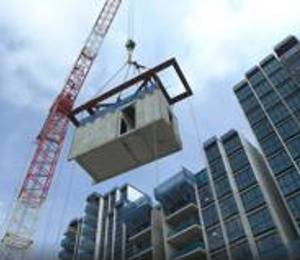
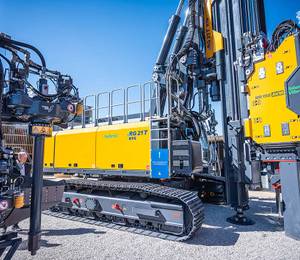
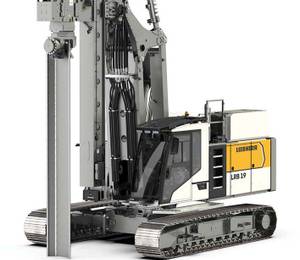
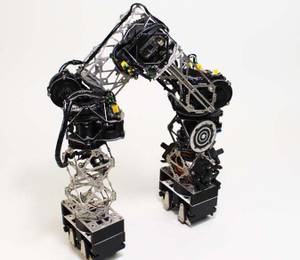