During the Liebherr international construction trade press tour 2024, held recently in late October, the group shared more details about its sustainability strategy and showcased a number of lower-emission drive solutions as an alternative to the diesel combustion engine.
“We want to provide our customers with carefully considered, economical and long-lasting viable alternatives to fossil-fuel engines, so that they can achieve both their performance objectives and their emissions targets,’ said Philipp Suhm, head of engineering technology coordination at Liebherr.
Speaking to the trade media, Mr Suhm highlighted that the development work at Liebherr focuses on more than just the potential to cut CO2 emissions. Other aspects including technological maturity, availability of infrastructure, and costs of energy sources also determine how successful an alternative drive solution may be.
“A holistic and technology neutral approach is required for future drive technology development,” he said.
CO2 lever and technological maturity
To identify the largest possible lever for reducing CO2 in its products, Liebherr has had the emissions of its machines scientifically analysed for their entire life cycle – right from the point of raw material extraction through to production, all the way through customer operation and on to decommissioning and recycling. Based on this analysis, the greatest cuts by far could be achieved in the operating phase. Therefore, Liebherr is concentrating its efforts and resources on developing alternative drive technologies for construction machines, cranes and mining machines.
The breadth of alternative drive technologies is wide and Liebherr is exploring everything from HVO (hydrogenated or hydrotreated vegetable oils) and e-fuels to electrical solutions incorporating mains or battery operation and even hydrogen and ammonia. Some of these technologies are established enough that they are already in use in the short to medium term – including HVO, electric and hydrogen-based solutions. For other approaches, like ammonia, work is still needed to refine the technology.
Infrastructure and costs
When it comes to operating machines with alternative drives, the requisite infrastructure is a decisive factor. In the case of hydrogen, in particular, an extensive supply network and adequate filling stations are required. Electric drives also need a sufficient supply of charging stations. Liebherr is actively working to overcome these challenges. Together with its partners, the group is developing innovative solutions for mobile refuelling and a reliable supply of green hydrogen.
The costs of the energy sources used are another key factor to be considered in the development of alternative drive solutions. According to Liebherr, countless studies agree in their predictions that ammonia will in the future be the most cost-effective, and e-fuels the most expensive, energy source. The costs for HVO, electric drives and hydrogen-based solutions fluctuate between these two poles.
In that regard, the production of HVO is generally more cost-intensive than conventional diesel. Hydrogen technology, especially fuel cells and the infrastructure for distributing hydrogen is, by comparison, even more expensive at present. In the case of electric drives, the batteries required are cost-intensive, plus their performance can decrease over time, meaning they have to be replaced.
In light of the influencing factors described, Liebherr is currently focusing its defossilisation efforts on its machines, especially on HVO, electric drives and hydrogen-based drives, so that they can offer a varied choice of drives to best suit the customer’s individual requirements, depending on the type and location of application of the machine in question.
HVO and electric drives
Most Liebherr diesel engines are already HVO-ready, meaning they can also be powered by hydrotreated vegetable oil, cutting CO2 emissions by up to 90%. For example, the group’s facilities in Germany (Liebherr-Hydraulikbagger GmbH and Liebherr-Werk Ehingen GmbH) now deliver all machines with a tank filled with HVO.
In terms of electric drives, the group offers a variety of solutions, such as the battery-operated L 507 E wheel loader, the ETM 1205 concrete mixer with electric drum drive, and the unplugged series of Liebherr deep foundation equipment, as well as various mains-operated machines as the material handling machines LH 40 M Port E and the LH 26 M Electric Industry. All these models produce zero emissions in operation; and if powered by renewable energy, they are completely carbon neutral in operation.
Additionally, the Liduro Power Port (LPO) from Liebherr delivers the energy supply needed for the battery-powered machines. This mobile charging station allows electrically powered machines to be deployed even in fields of application that lack the necessary infrastructure.
Liebherr is also working on pioneering solutions for the electrification of large machines in the mining sector, in collaboration with Australian company Fortescue. The latter recently took delivery of a total of 475 Liebherr mining machines that produce zero local emissions, making it the biggest contract in Liebherr’s 75-year history.
Hydrogen drives
Further to this, Liebherr is developing a hydrogen motor that facilitates zero-emission operation of machines and – if the hydrogen is generated using green electricity – can even be completely carbon-neutral in operation. In July 2024, the group introduced the L 566 H wheel loader, the world’s first prototype of a large loader with a hydrogen motor.
Over the course of the development of the hydrogen wheel loader, Liebherr commissioned its own hydrogen filling station at its Bischofshofen, Austria plant. In partnership with the filling station developer Maximator Hydrogen, Liebherr is optimising its mobile refuelling options to allow construction machines to be supplied with hydrogen while on the building site. In addition to this, Liebherr is working with MPREIS to establish a reliable supply of green hydrogen, generated from wind, hydro or solar energy.
At the press tour, the media had the opportunity to see the hydrogen-powered wheel loader in person. Liebherr, in partnership with construction company Strabag, is currently testing the machine in practical applications at a quarry near Graz, Austria. The project began in September 2024 and is expected to last for about two years. Over this period, Liebherr will gather valuable data in a field trial, which will serve to validate the use of hydrogen motors in large-scale construction machines.
The potential of ammonia
Liebherr is also researching the use of ammonia in alternative drives. Although the prospect of ammonia as a sustainable energy source is still some way off, the group believes it has the potential to play a major role in powering the world in the future. Plus, ammonia produced using green energy can serve as an efficient medium for transporting hydrogen.
Going forward, Liebherr will continue to fine-tune its drive technologies and open up new ways of reducing CO2 emissions throughout the entire life cycle of its products. In close collaboration with its partners and the continuous further development of the infrastructure, the group is making significant investments in research and development work in all areas of drive technologies – both now and in the future.
“We know there isn’t a one-size-fits-all drive technology,” concluded Mr Suhm. “We’re working with an open approach to technology on a wide range of different drive technologies across our portfolio of products.”
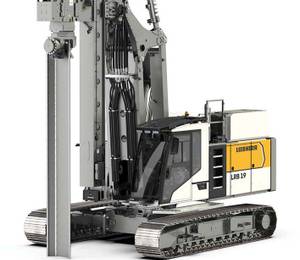
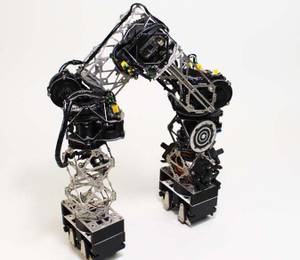
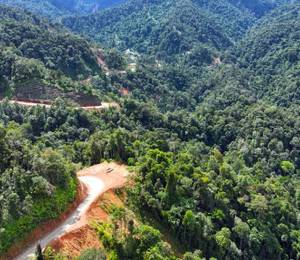
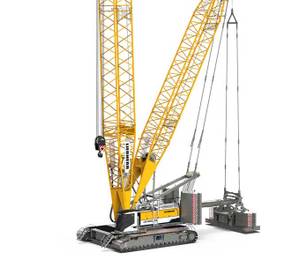
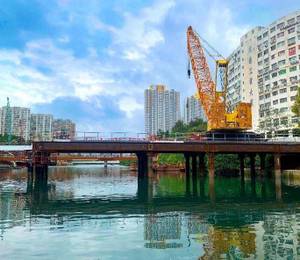
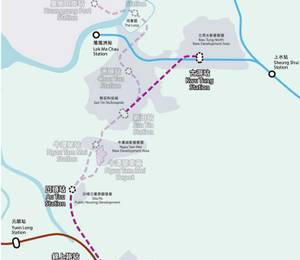
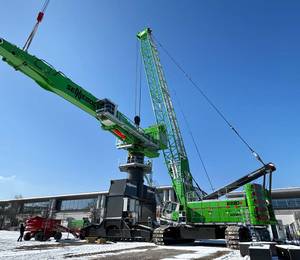